Senior Design Project — Fish Tank Monitor
Award: Hoffman Construction Process Excellence
An all-in-one aquarium monitoring system I co-developed to track water quality parameters like nitrites, pH, temperature, and hardness using a pump-fed color sensor and temperature probe. Features include an e-ink display with a dial/button interface, custom PCB integration, and a 3D-printed, fish-safe enclosure. Designed for ease of use and accuracy, with future expansion planned for wireless alerts and remote access.
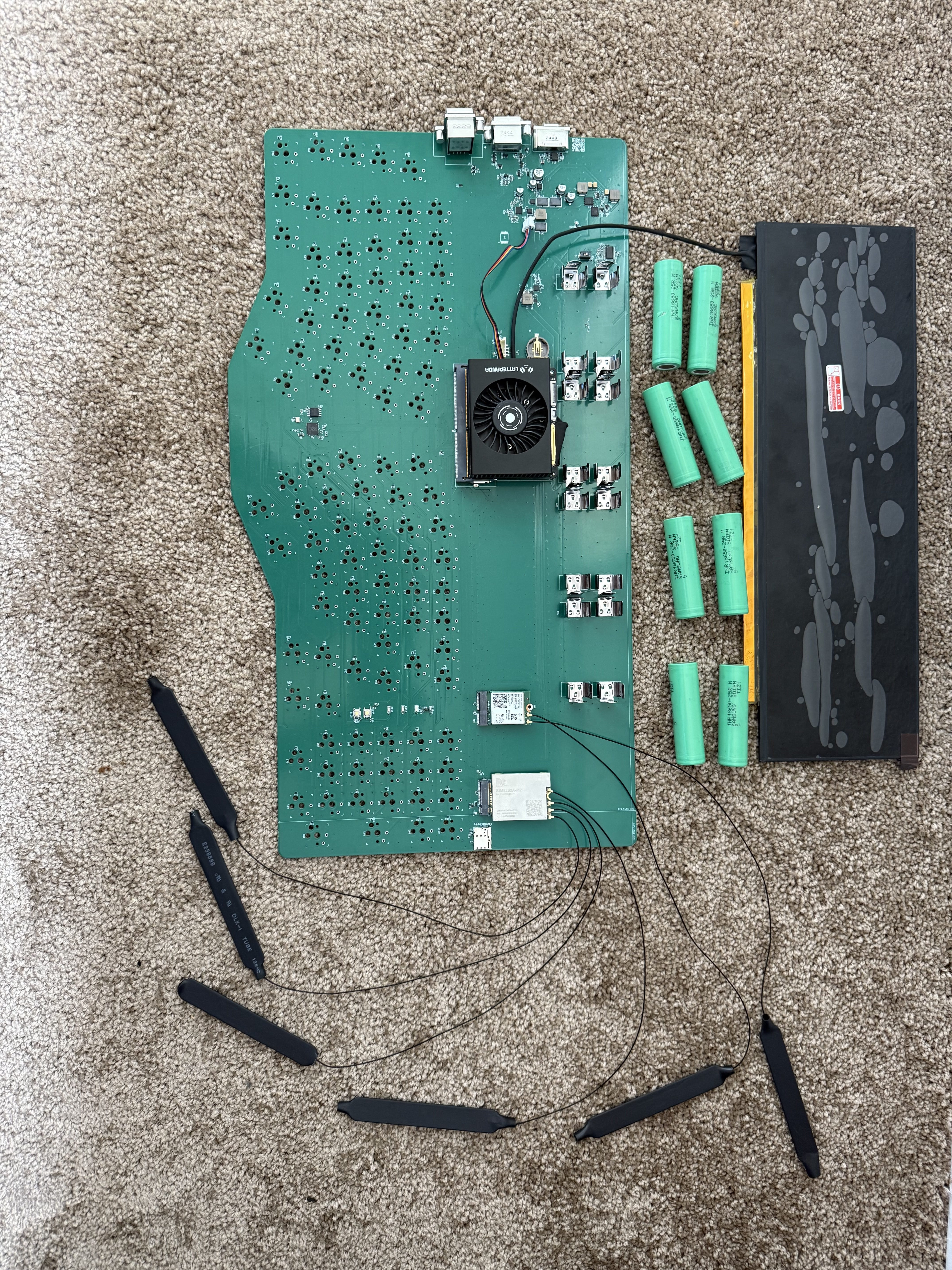
Remote-Access Desktop Terminal (R-DAT)
A custom hardware project designed to create a portable keyboard-terminal that interfaces with a LattePanda Mu for remote desktop access from anywhere in the U.S. Over a 10-week design cycle, I engineered a custom PCB and battery management system, implemented USB-C PD at 20V/2A, and planned multi-stage voltage regulation (16.8V, 10V, 5V, 3.3V). The device features a water-resistant enclosure and a fully custom keyboard layout. Despite setbacks including supply chain disruptions, PCB manufacturing delays, and a non-functional first revision, this open-source project demonstrates my end-to-end hardware development skills, iterative problem-solving, and commitment to continuing the work beyond the initial course deadline.
The entire project source is avalable here.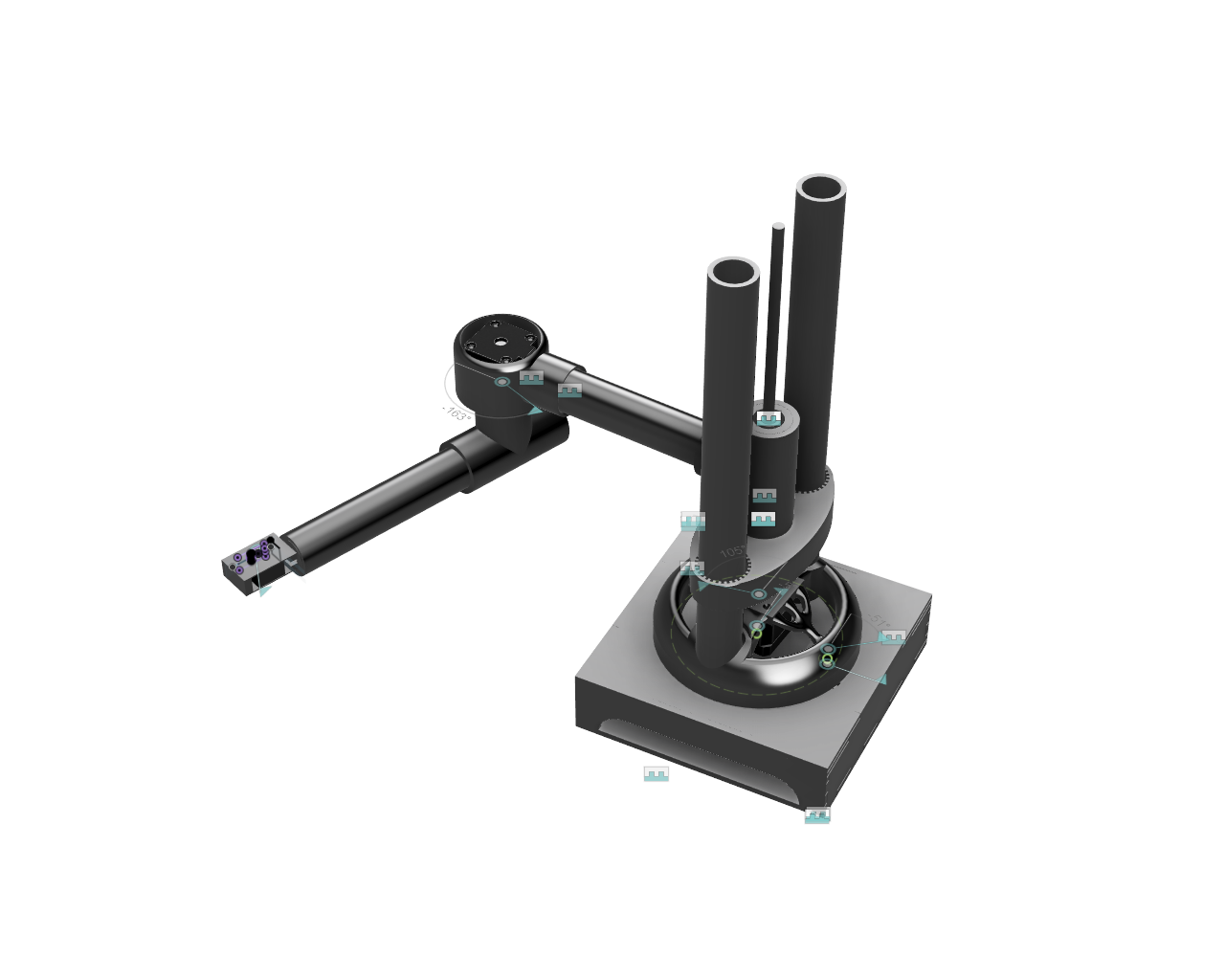
SCARA Robotic Arm with G-Code Parsing
Collaboratively designed and built a SCARA-style robotic arm capable of interpreting and executing G-code commands to draw images with tool-changing functionality. The system uses stepper motors for X, Y, and Z motion, and a servo motor to control the active tool, with the entire base capable of powered rotation. A custom Python script parses G-code to dynamically adjust movement, speed, tool, and drawing height. Our arm excelled in speed and seamless tool switching, with reliable motor control powered at 24–36V. While accuracy limitations prevented the arm from producing precise long lines, this first prototype lays the groundwork for future refinement in structural rigidity, motor cooling, and motion precision.
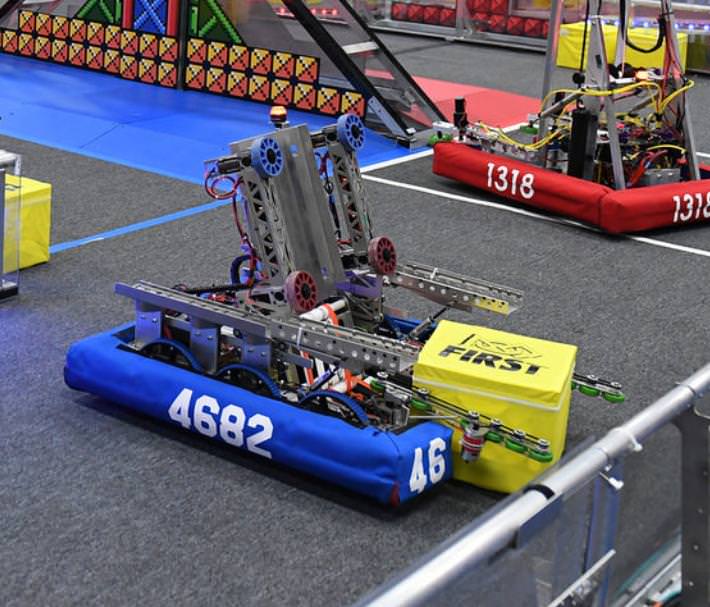
First Robotics Team 4682
As a core member of FRC Team 4682 CyBears, I served as Lead of the Electronics and Software teams for three years, Assistant Captain for one year, and Team Captain in my final year. I played a central role in designing, building, and programming competitive robots, gaining hands-on experience with tools such as drill presses, 3D printers, band saws, soldering irons, and a Tormach CNC. I developed CAD models in Fusion 360 and wrote control software using Visual Studio Code. Beyond technical contributions, I mentored younger members, coordinated build schedules, and led strategy during competitions. This experience was foundational to my growth as both an engineer and a leader.
Leviton Microphonics
Explore the presentation by flipping through the slides below:
Datalogic VAL
Explore the presentation by flipping through the slides below: